A brief insight into the development of k-data
Our story began in 2005 with a professionally rebuilt engine that kept misfiring in the partial load range. The original DME1.2 engine control unit did not report any faults, which meant that we were reliant on our own measuring devices. Despite intensive cooperation with various specialists, including an authorized workshop, we were unable to find a solution to the problem. This frustrating experience led to the need for an open system. A system that works on the standard wiring harness and is compatible with existing sensors so that all live data and parameters can be viewed and adjusted. After we had worked intensively on this challenge, the tuners at the time told us that a free programmable control unit in plug-and-play format was not technically possible. This skepticism strengthened our motivation to develop such a system. We wanted to overcome the difficulties and develop a solution that would be equally useful to us and others in similar situations.
The first version of our free programmable engine control unit kdFi (Kastner Datatechnology Fuel Injection) was born.
From the idea to series production:
Development
Developing new PCBs is very time-consuming work. We therefore try to use components that are available in our machines or can be processed with them as early as possible in the layout of the circuit board, enabling us to manufacture all assemblies from the first prototype to series production in our own in-house production facility.
(Image: PCB layout in the home office)
(Image: PCB layout in the home office)
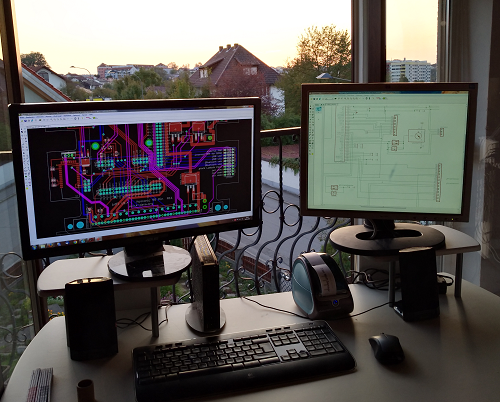
Prototypes
In order to maximise our flexibility and shorten the development time, we decided a few years ago to purchase our own machines for assembling our PCBs.
(Image: Stencil printer for solder paste)
(Image: Stencil printer for solder paste)
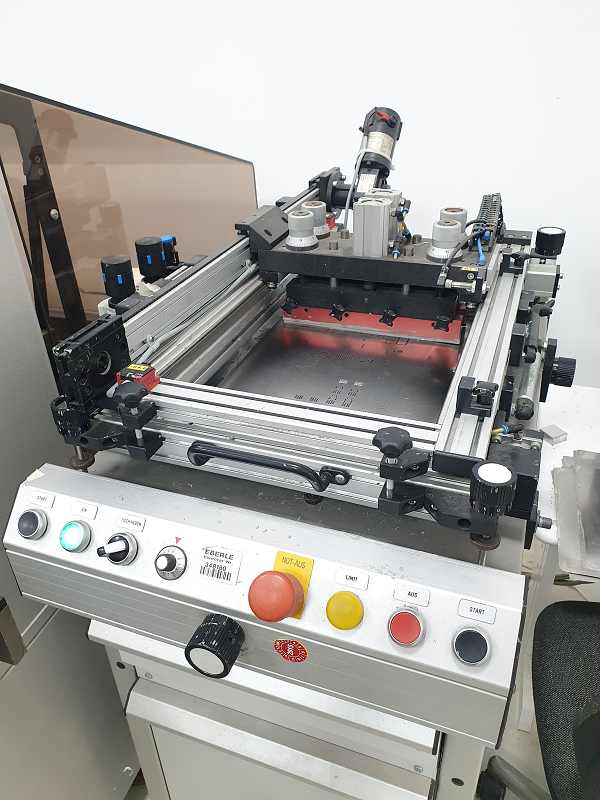
Series production line
The gentle soldering process in our vapour phase soldering system is important to us in order to minimise the thermal load on the semiconductors and at the same time achieve an optimum result for different component sizes on a circuit board.
We rely on proven technology from Siemens, IBL and other industrial suppliers.
(Image: IBL SLC300, Siemens Siplace CF, Siemens MS128)
We rely on proven technology from Siemens, IBL and other industrial suppliers.
(Image: IBL SLC300, Siemens Siplace CF, Siemens MS128)
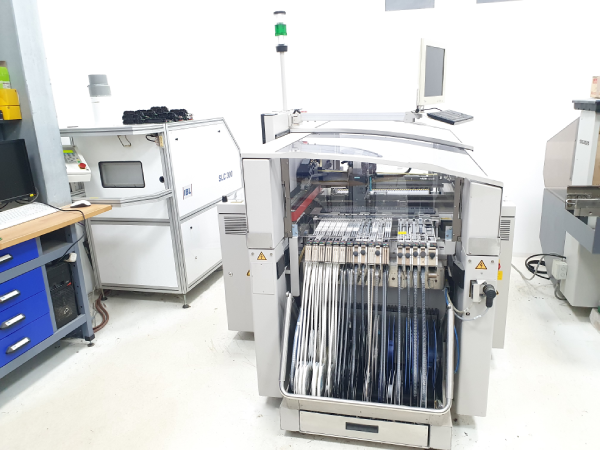
Storage
Components with difficult availability are stored dry and vacuum-packed so that they can be processed at any time if required.
This gives us sufficient time to find a future-proof replacement for discontinued components.
By avoiding ‘just in time’, we were able to deliver at all times, even during the chip crisis.
(Image: Feeder with component belts)
This gives us sufficient time to find a future-proof replacement for discontinued components.
By avoiding ‘just in time’, we were able to deliver at all times, even during the chip crisis.
(Image: Feeder with component belts)
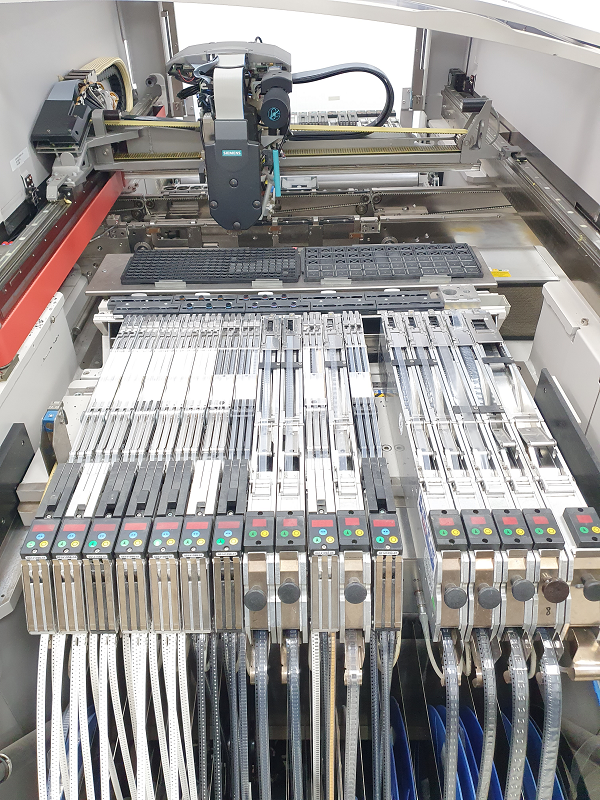
Function test
Thanks to the exhaust extraction system in our workshop, we can check the function of every single control unit in series production on the engine and also carry out measurements and tests during the development phase as realistically as possible.
(Image: BMW E46 with M52TU engine)
(Image: BMW E46 with M52TU engine)
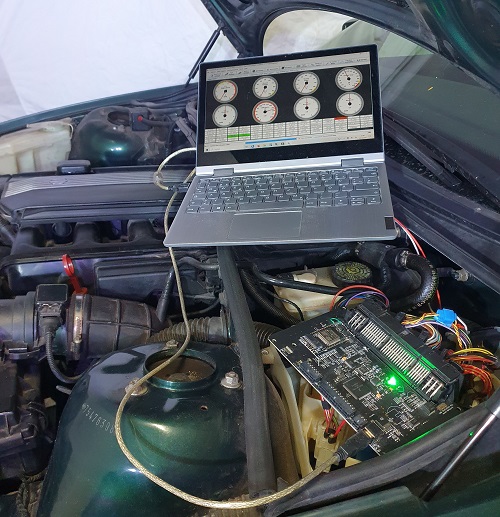
Shipping
In order to deliver the orders to our customers as quickly as possible, our products are immediately available according to the stock level stored in the shop.
Worldwide dispatch by DHL takes place daily, with only a few exceptions.
(Image: Packaging room)
Worldwide dispatch by DHL takes place daily, with only a few exceptions.
(Image: Packaging room)
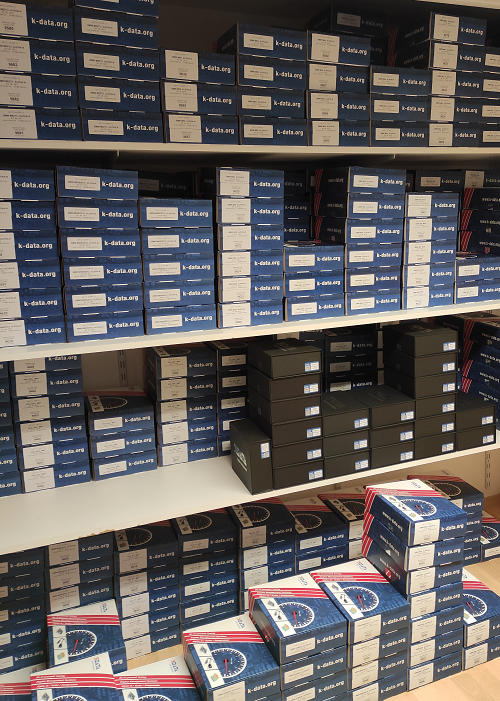